The potential of additive manufacturing — 3D printing — to help build a better world is expanding all the time, from customized surgical implants to parts for commercial jet engines. Additive manufacturing technologies, specifically additive construction, is poised to impact global efforts in energy efficiency, as well as safe and affordable housing.
“In additive manufacturing the opportunities are unlimited,” said Ashley P. Thrall, the Myron and Rosemary Noble Associate Professor of Structural Engineering in the Department of Civil and Environmental Engineering and Earth Sciences and project lead. “This includes 3D printing entire buildings. With additive construction, we can rapidly build structures using less labor. Components are assembled one layer at a time to exacting standards. Our interdisciplinary team is exploring ways to print reinforced concrete walls that are strong, more energy efficient, and cost less to produce.”
Thrall and David B. Go, the Rooney Family Collegiate Professor of Aerospace and Mechanical Engineering, direct the Notre Dame team. They are working in collaboration with Eric Kreiger, a research structural engineer, and Brandy Diggs-McGee, research mechanical engineer, at the U.S. Army Corp of Engineers (USACE), Engineer Research and Development Center (ERDC), Construction Engineering Research Laboratory (CERL).

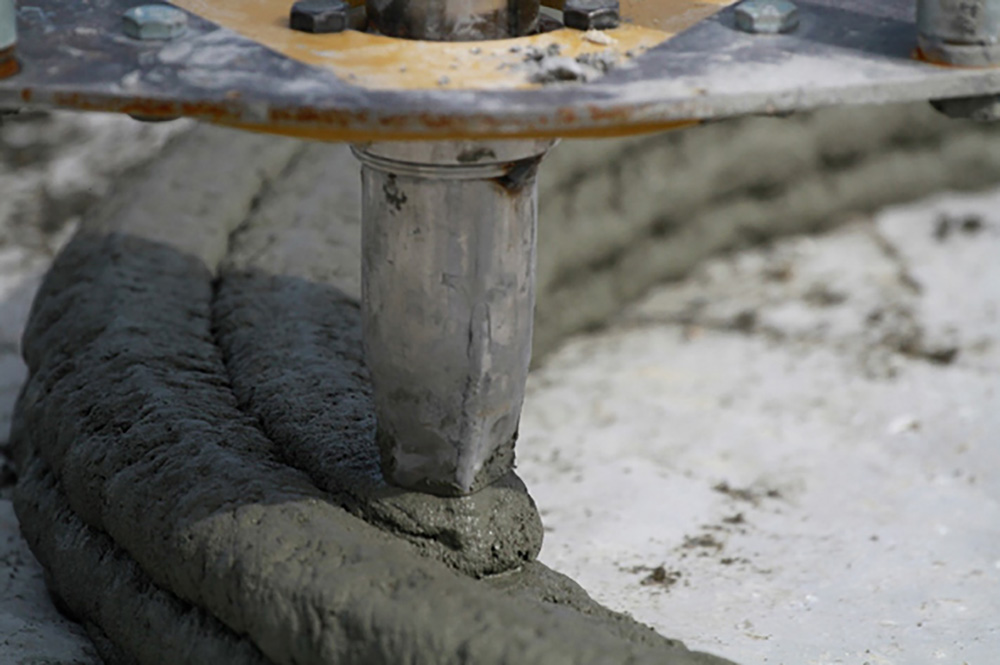
Residential and commercial buildings account for approximately 40 percent of the country’s energy needs — more than transportation or industry. The challenge is finding ways to increase energy efficiency in structures beyond using LED lights or high-efficiency furnaces. “We are working to advance building construction by exploring wall designs that can be easily 3D printed while providing sufficient strength but, when included in a building, require less energy to heat or cool,” said Go.
CERL has been researching the use of additive manufacturing technology for construction since 2015, making their research laboratory and team ideal collaborators on the project. Additive construction in general has advanced as much in those five years as other fields have advanced in the last two decades. What began as a few studies being conducted by a handful of disconnected companies around the world has developed into a global interconnected network of researchers and institutes.
“3D printing allows us to manipulate design criteria quickly and to simulate and analyze the results before materials are used for construction,” said Diggs-McGee. “Utilizing additive construction technology as a building platform in research aids in the reduction of intensive labor hours, logistical costs, material usage, and a project’s time-to-completion while also giving us a comprehensive overview of a system.”
“Additive construction enables the construction of a full range of structures that are structurally and functionally optimized,” said Kreiger. “Concepts that were once deemed unrealistic can now jump off the sketchpads of architects and engineers and become reality.”
This material is based upon work supported by the U.S. Department of Energy’s Office of Energy Efficiency and Renewable Energy (EERE) under the Building Technologies Office, Award Number DE-EE0009070.
— Nina Welding, College of Engineering